NB48 2.0 Behind the Design - Part Two - The Details
This is the second article in our three part series about the all new Tekno RC NB48 2.0 1/8th Competition Nitro Buggy. Here we will talk about some of the new features and innovations in more detail.
NB48 2.0 Differentials
Where do we start? Well, just about every car design or kit build starts with the differentials. They are the foundation that everything else is designed and built around. The main objectives with the new differentials were higher oil capacity, smoothness, and durability.
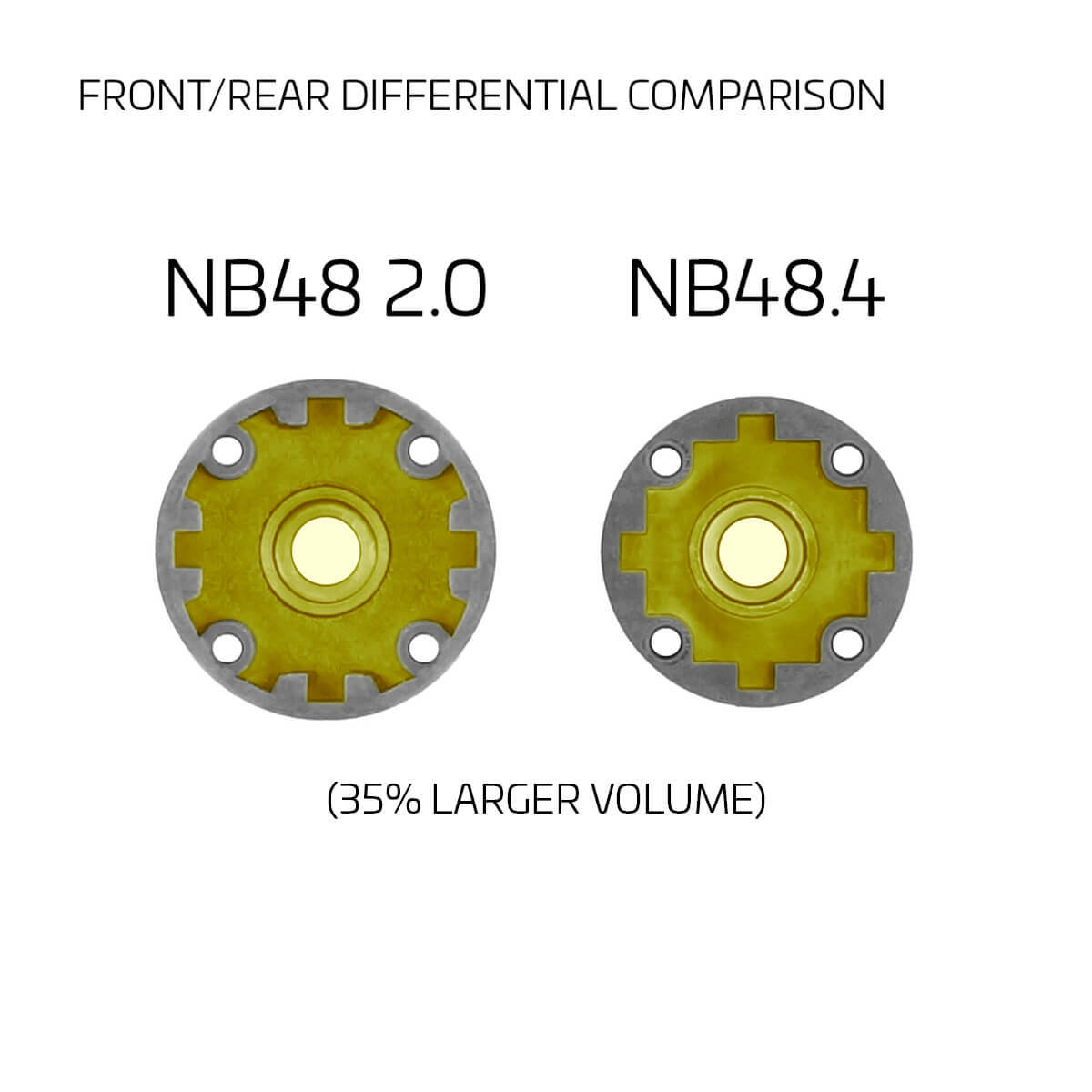
First, the 2.0 differentials hold ~35% more oil compared to the NB48.4 units. Of course this helps with consistency during long mains, but it also extends the time between rebuilds. During our long testing period, we didn’t experience any ‘cooked diffs’ and the oil was exceptionally clean compared to anything else we’ve seen. But oil capacity alone is not responsible for this.
The second objective was smoothness. After years of improving the performance of our previous differentials, we took that knowledge and put it to work here. We decided on a slightly finer internal gear pitch that meshes better and produces less heat. Less heat results in greater consistency, virtually no fade, and the exceptionally long oil life we observed during testing.
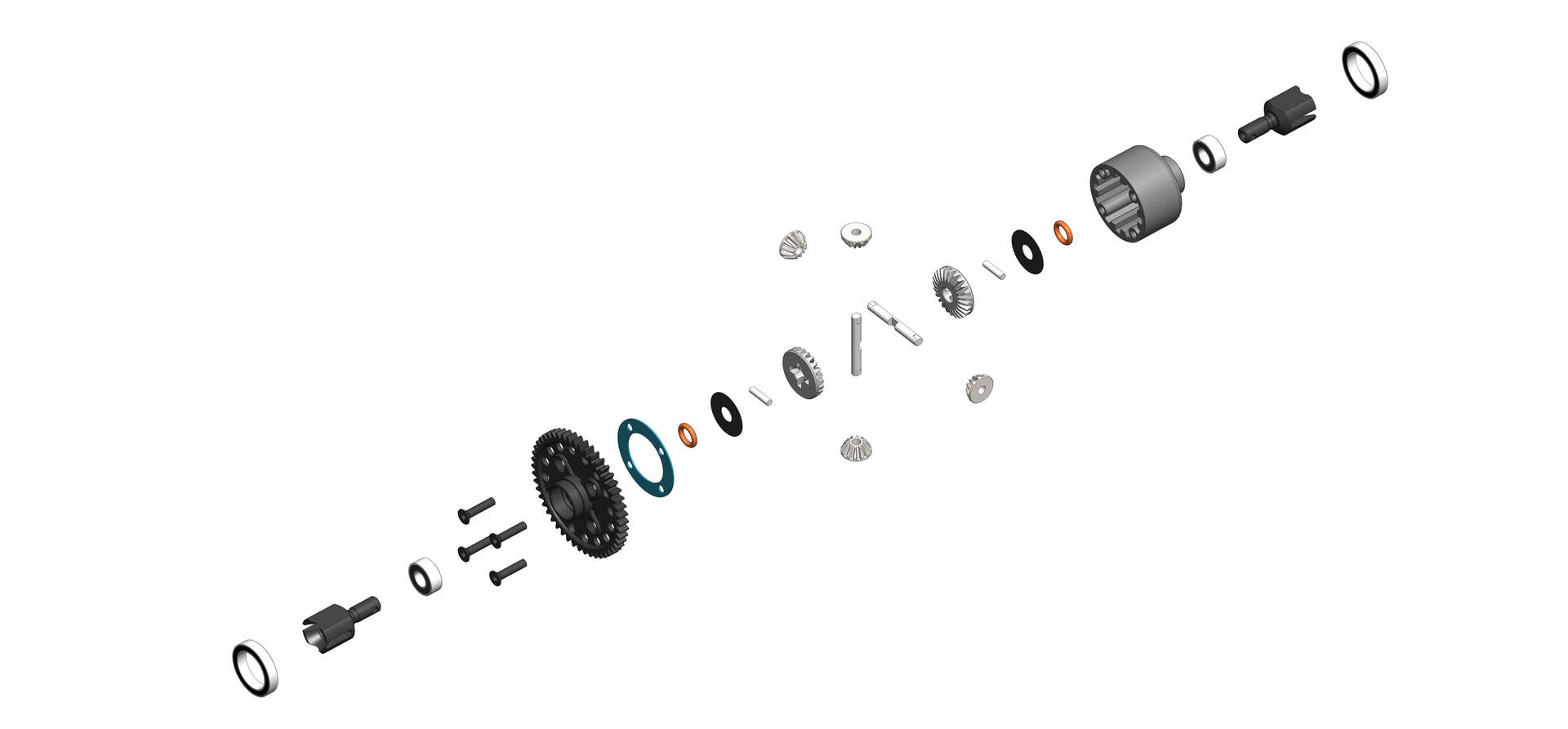
To further reduce heat build up and improve consistency, we developed a compact double-bearing supported center differential. Up until now, 1/8th scale RC differentials have had steel outdrives spinning inside steel sleeves, either in the spur or ring gear, or in the diff case. Metal on metal contact, even when properly greased or aligned, produces excessive heat. We have mitigated this issue by using ball bearings in place of the traditional sleeves to fully support the center outdrives and completely eliminate the metal to metal friction between the outdrives and the mating parts.
Differentials endure some of the most extreme forces during a run and any diff issue pretty much ensures you're not going to win the race. With these changes we feel we've made them even stronger. During our year of testing, the gears, pins, diff cases, and outdrives certainly stood up to all of the abuse we threw at them.
NB48 2.0 Bulkheads
The larger differentials meant that new bulkheads were required. We used this opportunity to implement some other features we’ve had on our list for a while, such as improving access to the front and rear differentials during maintenance. Let’s face it, if the diffs are hard to access you are less likely to service them or make a setup change. As mentioned above, time between maintenance on the diffs is much longer, but when you need to make that quick setup change before the A main, you’ll appreciate how quickly and easily they are to access.
Inside the bulkhead you’ll find a larger inner bearing supporting the diff pinion gear. The bearings were also moved further apart, virtually eliminating pinion bearing failure. As was the case with our previous vehicles, we spent considerable time fine tuning the tolerances and gear mesh to reduce the need for complicated diff shimming. Similar to our other vehicles, the bulkheads are completely sealed off to dirt and dust with precise fitting bottom and outer bulkhead covers. This feature is often overlooked, some might even say unnecessary, however, it’s one less thing to worry about when racing out in the elements.
The sway bar system is all new and now rides on ball bearings. Smooth sway bar action is ensured without having to mess with set screws and imperfect adjustments. There will be plenty of sway bar options available at launch, consisting of 2.0-2.8mm front, and 2.2-3.0mm rear sway bar options.
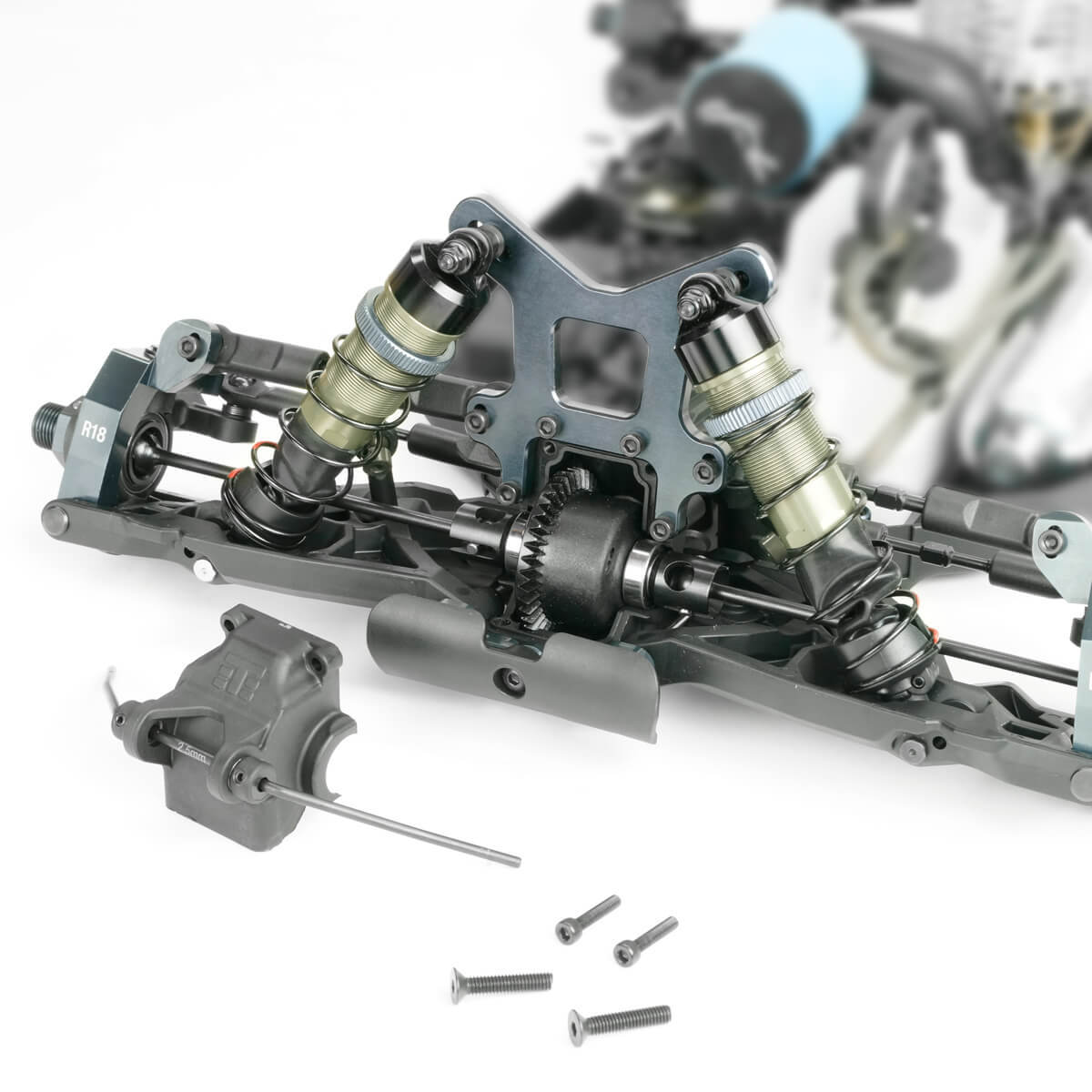
NB48 2.0 Chassis and Radio Tray
We went with an all new 3mm, fully CNC machined, 7075 aluminum chassis which is hard anodized for long wear. The new chassis is one millimeter thinner but also substantially wider to reduce twitchyness and improve handling and flex characteristics on rough tracks.
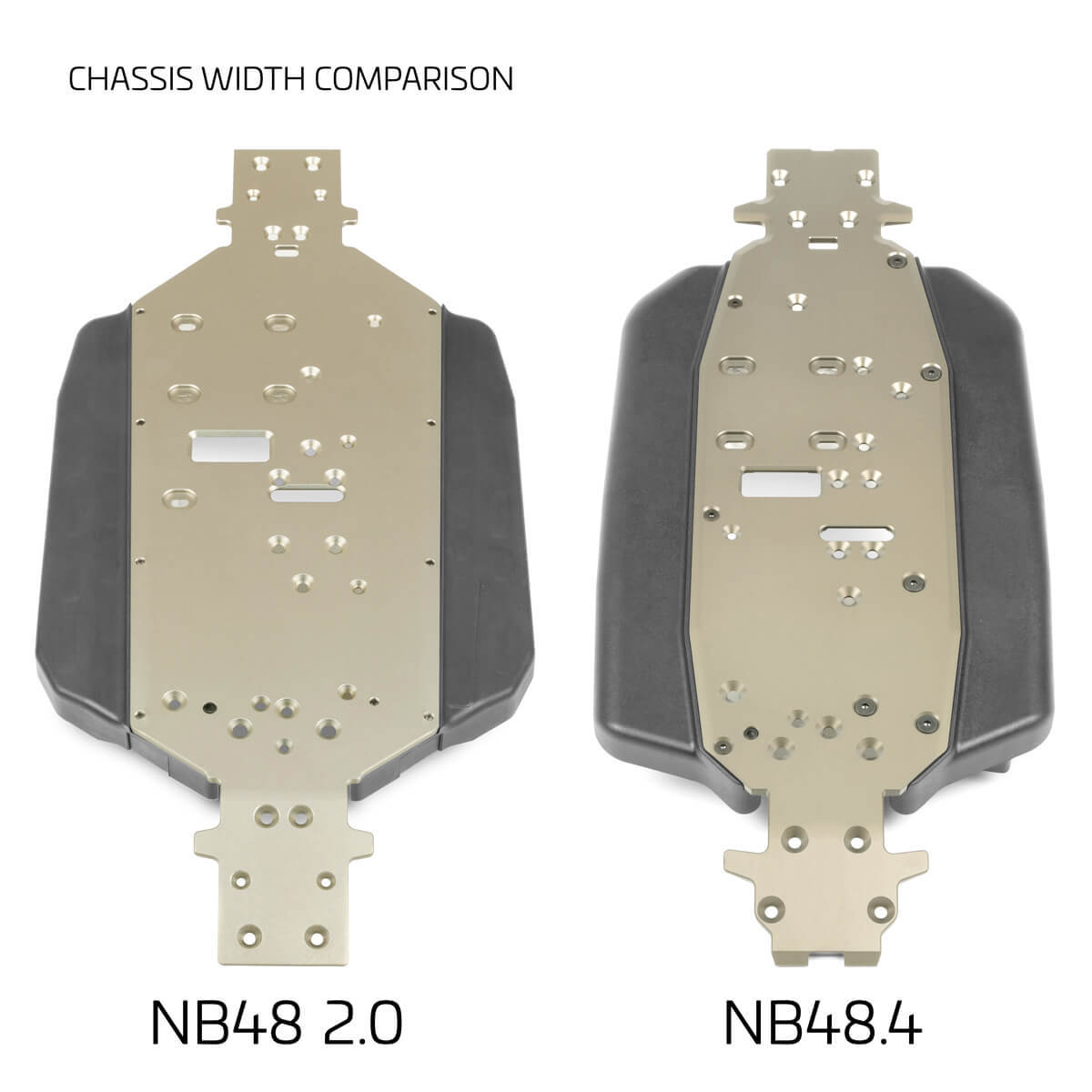
With a traditional rigid radio tray, the right side of the buggy is stiffer and ends up flexing significantly less than the left side, where only the engine and fuel tank are mounted. We realized this with our previous nitro vehicles and made the decision early on to scrap the ‘traditional’ radio tray, opting for completely independent receiver/battery boxes and servo mounts. While there are a few more screws to loosen to get the radio equipment out, it’s the on-track performance and side-to-side balance of the buggy that reaps the benefit here.
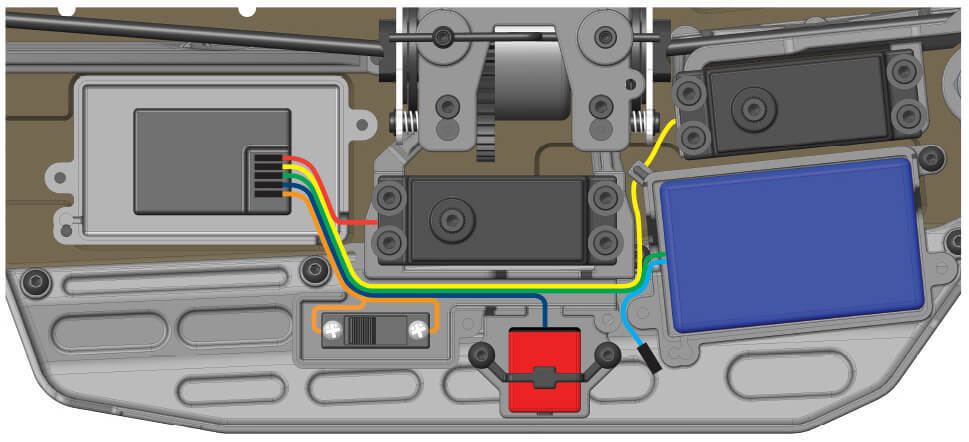
Each electronic component has its own space on the chassis to minimize their influence on chassis flex. Up front, the steering servo is mounted to the front chassis brace. The battery box is integrated into the right side mud guard to keep the center of gravity as low as possible, while still maintaining independence from the other components.
You’ll find the throttle servo mounted directly to the center differential assembly. This not only improves braking efficiency and consistency, but it prevents the servo torque from pulling the center diff assembly over and altering the clutch bell/spur gear mesh during a race. Throttle servo longevity is also greatly improved.
In the back, the receiver box is sunken into the chassis for the lowest possible center of gravity. We designed the receiver and battery boxes to be the same dimensions so you can install the battery either in front or in the back. This can help you dial in more front or rear grip if your driving style or track conditions require it. The rear receiver box is also completely removable if you would like to further reduce weight by combining the receiver with a compact battery in front.
NB48 2.0 Suspension Geometry
There’s more to the new front and rear geometry of the NB48 2.0 besides the ultra narrow pivot design. When designing the geometry this time around, we decided we would go back to a standard pivot to lengthen the arms for better bump handling. One thing led to another and the question was asked, “how long can we make them?”
The only way to lengthen the arms beyond what the market currently offered was to narrow the pivots as much as possible. So the bulkheads were redesigned with a fresh approach to mounting the pivot blocks in order to maintain durability. The theory was simple - longer arms will make the buggy easier to drive, provide superior bump handling, superior jump landing, and allow the vehicle to be pushed much harder than before without getting in trouble.

The front end was especially challenging as we had set some lofty design goals for ourselves. There are a few different types of front end geometry currently utilized in offroad RC. The pillow ball (e.g. Mugen), the inset C-hub (e.g. Kyosho), and the outset C-hub (older Losi). It is apparent that the pillow ball and inset C-hub allow for the longest arms. But these systems sacrifice level dog bones (i.e. dog bone plunge-in or pull-out), or offer a less than optimal scrub radius (i.e. offset inside or outside the center of the tire).
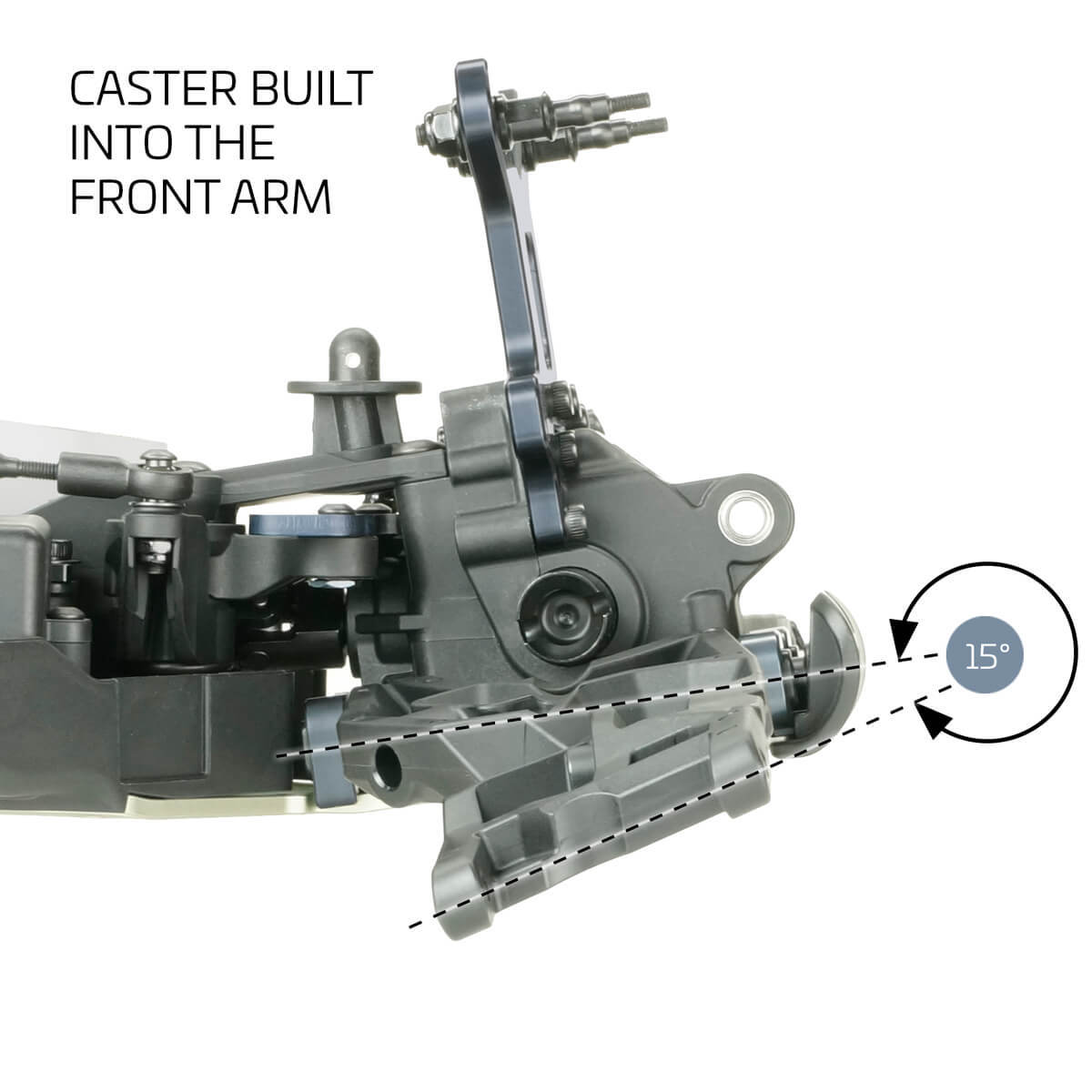
The design goals were zero plunge, zero scrub, extreme durability, and the longest front arms on the market. After many iterations, we had an idea to twist the end of the arms for the needed clearance to lower the axle. The same trick allowed for a longer arm and enough room to place the spindle/kingpin axis on the same plane as the outer hinge axis, producing a zero offset, zero scrub steering system that is as durable as an outset C-hub design. On the track, this translates to smoother cornering and direction changes with exceptional mid-corner bump handling.
The rear suspension geometry has also seen significant changes along with a few new ideas and adjustments. As with the front arms, the rear arms have been extended past what is currently available on the market. All the benefits mentioned earlier about longer arms also apply here.
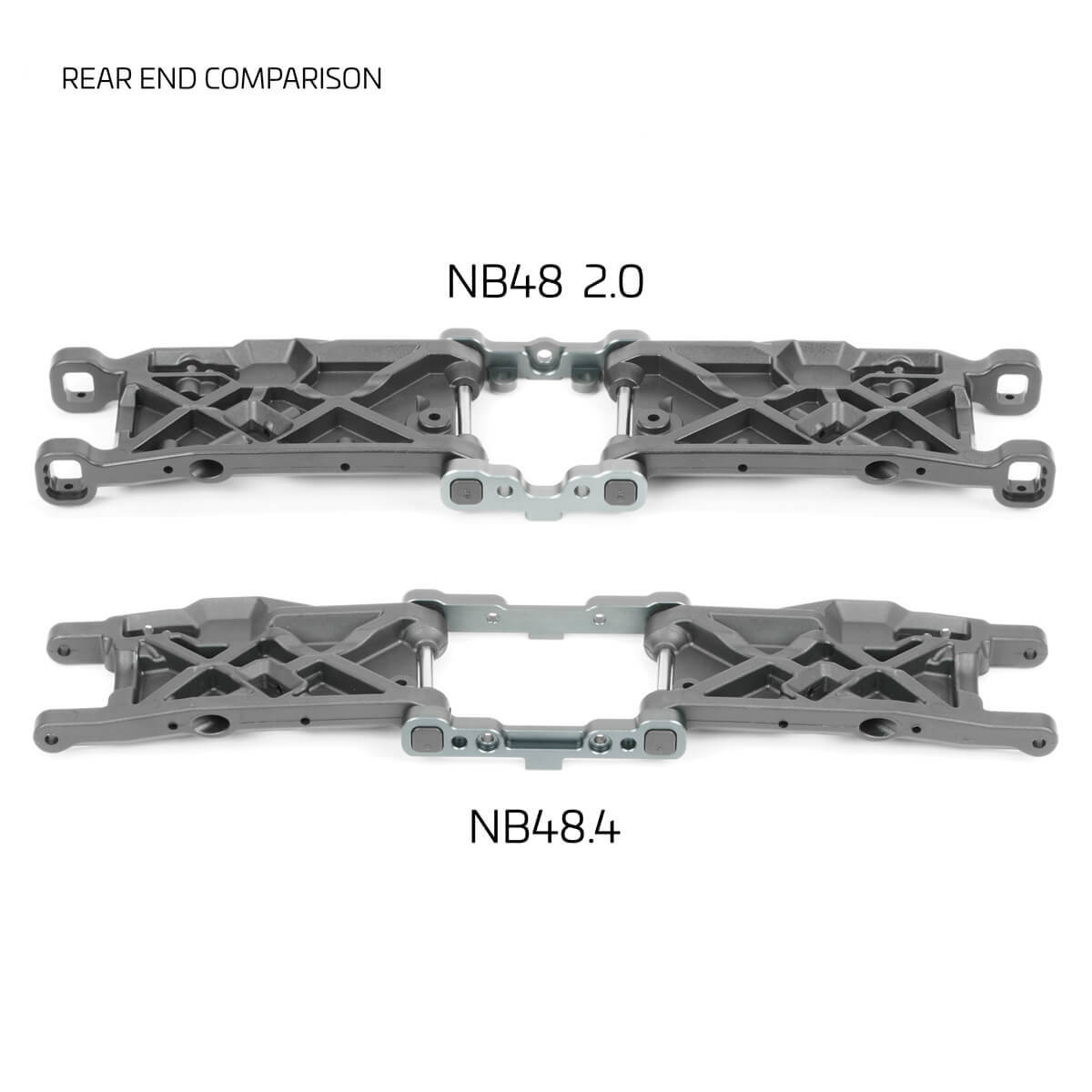
RC racing has become more advanced and competitive over the years so it’s essential that new vehicles provide innovative adjustments to give you an advantage. The NB48 2.0 features a unique arm insert system that allows not only static toe adjustment at the hub, but also active toe adjustment.
The outboard static toe adjustment is useful for adjusting traction without changing the wheelbase or the angle of the inner hinge pin. Or you can use it to change the wheelbase or angle of the inner pin without changing static toe. The options are there to find the optimum setting for you.
Our new active toe system doesn’t require a second link or an additional spindle, just change the inserts according to what you need. You can add active toe in for more traction out of the corners on tight or loose tracks. Or choose active toe out for enhanced corner speed or bump handling on higher speed, higher traction layouts. It’s the type of innovation people have come to expect from Tekno RC.
NB48 2.0 Full Reveal Coming Up
1/8th nitro buggies represent the F1 of offroad RC. We take pride in innovation and forward thinking because the available space for copycats shrinks every year. The evolution never stops, and if you stand still for too long, you’ll get run over. We don’t do things differently just to be different, it’s more that we refuse to settle for ‘good enough’.
We took our time because we feel our loyal customers shouldn’t be beta testers. Our goal was to present a new platform that just works out of the box, one that doesn’t need parts from another car to make it competitive. After many years of intricate design work and intense testing, we haven’t just refined the NB48, we’ve redefined the NB48.
In our next article we’ll reveal all of the goodness that will put the NB48 2.0 at the top of your list. Pre-orders for kits and spare parts are available now at our website and through our worldwide network of dealers and distributors.